From Voltaire, to Confucious, to Shakespeare, throughout history luminaries and leaders of all stripes have ruminated on a recurring theme – the value of good enough being good enough.
Or, if you prefer, not letting perfection be the enemy of the good. Today it’s a concept adapted for a host of applications and process-oriented tasks. In finance, it’s the idea that waiting for the ideal opportunity to invest X sums could cost said investor more money over time as the required rate of return must increase sharply to offset delayed investment.
For the business of precision measurement, “good enough is good enough” has value, too. Not in terms of the equipment used – it’s never wise to purchase a subpar product – but in terms of the accuracy required to get the job done in a timely fashion. Too often in 3D metrology this simple precept is overlooked; manufacturers, in effect, bring too much precision and spend too much time on a task that could have been achieved with lower, but fully acceptable accuracy in faster time.
Focus ‘in Focus:’ More than the Darling in Construction
In an increasingly competitive economic landscape, “good enough is good enough” is a concept that’s fast gaining ground as manufacturers from shipbuilding and automotive, to general large-part assembly for many industries, look to save time, reduce costs, improve safety and increase throughput. For many, the time has come to rethink what the “right tool for the right job” really means.
While not marketed as heavily for this specific target audience, the FARO Focus Premium Laser Scanner, known broadly for its architecture, engineering and construction applications, is also a fully viable solution for a variety of 3D measurement tasks. Namely this breaks down into three subcategories:
- Enhanced Product Design and Engineering: When a product lacks CAD data, the Focus Premium can scan a large part or entire assembly with excellent speed, detail and accuracy to create a 3D model, ideal for reverse engineering purposes. This also allows users to take the 3D model and compare to reference data, noting when any deviations occur, useful for clearance checks as in train tunnel, or if a construction crane is street-legal width.
- More Efficient Production, Fabrication and Assembly: Scan complex machine components, use the resulting 3D CAD data and dimensional control for precise-fit off-site assembly as needed, or simply use the data for manufacturing documentation.
- Improved Quality Control and Part Inspection: Perform precise dimensional inspection of large, complex components such as bodyshells, turbines and ship propellers through a standard CAD comparison that you’re used to performing with other 3D metrology devices such as Laser Trackers or ScanArms. This is most useful for large vehicles, heavy machinery industrial and machinery assembly. Think: truck and trailer parts, tanks, and cranes, for example.
- Assembly Check: Use the 3D data to check a large-part assembly to understand whether all components are present, at the right position and orientation. The Focus Premium enables the shift from a pure human-based, visual check to a data based, traceable analysis.
The key to each of these applications is the above-mentioned speed and accuracy. 3D laser scanners like the Focus Premium operate at the threshold where most portable coordinate measuring machines (pCMMs) reach their large-part scanning limit. While they may exceed a Focus Premium in terms of accuracy, they are more cumbersome to re-position, and larger parts will take many re-positionings.
This speed-bulk challenge is also faced with products like the FARO Laser Tracker – ideal to check main geometries with higher accuracies – but less suited for tasks requiring lower granularity inspection. For instance, a customer that builds heavy duty logistic equipment must inspect the bodyshell before final assembly. With a tracker a task like this might take more than five hours to complete. Using a Focus Premium in manual mode the same task can be completed in as little as 20 minutes for the entire workflow, a more than 90% decrease.
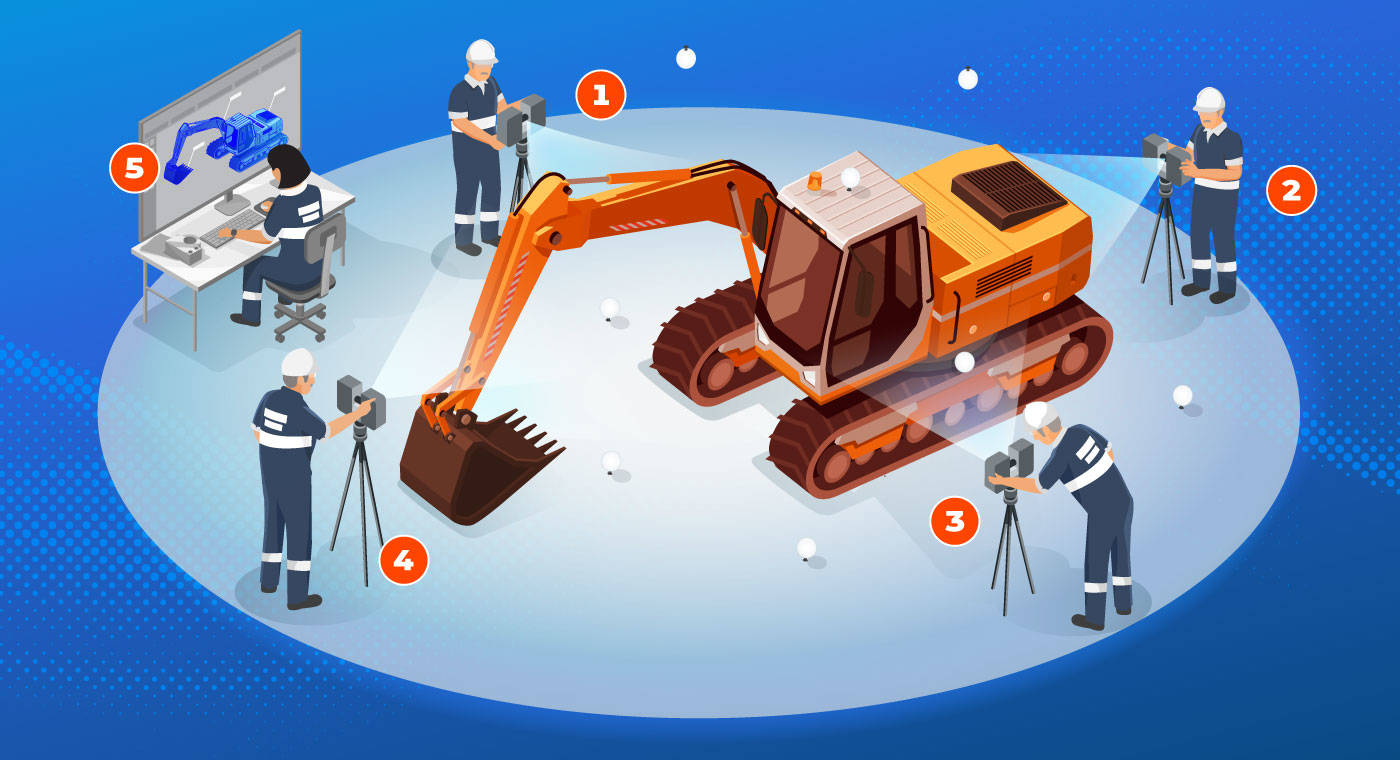
In another example, consider a heavy military equipment manufacturer who must perform a final check to determine that all parts are installed and at the right position. With the FARO Focus in manual mode (assuming four Focus Scanners and eight scanning positions) they can reduce this process from one full day (eight hours) to 20 minutes. Again, we’re talking about more than 95% time savings.
Of course, in automated mode, the process can be even faster. In that scenario all the user must do is to fix a set of scanners around the large part in question and take the scans automatically and in parallel with the click of one button.
Automated Data Capture – an Automatic Success
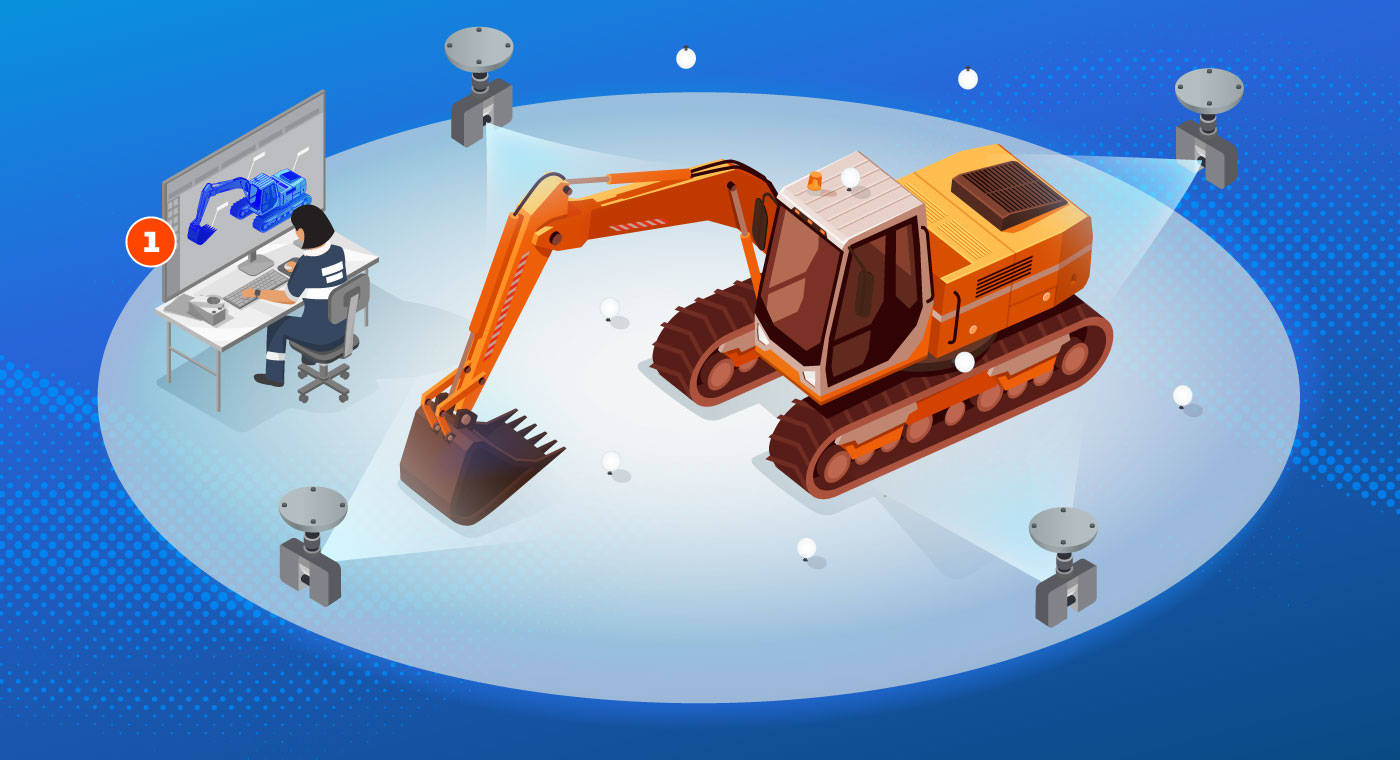
Under the hood is where the “magic” happens. That’s because for customers that manufacture large-scale products, the combination of the Focus Laser Scanner and FARO BuildIT Metrology Software, FARO’s 3D metrology software platform for alignment, build and inspection applications, is the 3D scanning solution that allows unprecedented speed of fully automated data capturing and analysis with an accuracy that is more than acceptable for most inspection applications.
Automated capture is the ability to take multiple simultaneous scans of a large part or assembly. The way it works is simple.
First, several Focus Laser scanners are fixed around the part to be scanned (on the wall or the ceiling). Next, a script in BuildIT, delivered with the installation of the system, activates all Focus scanners in parallel using a proprietary automation adapter device and transfers the scans through ethernet to a workstation.
Then, point cloud registration begins and un-used point clouds are deleted using a clipping box (remember that a Focus Laser Scanner generates a 360ﹾ point cloud in which much of that data is excessive for a metrology-centered task). Sphere targets (through FARO’s proprietary Traceable 3D accessory) aid in higher accuracy. The cleaned-up point cloud can then be compared with the CAD file where a final report is generated. All this workflow is completed automatically and is not only saving time, but also doesn’t require an expert to operate. Nor does it require all the same safety measures that are required for automated systems that involves industrial robots.
To be sure, manual workflows are also possible.
The biggest difference is that instead of simultaneous multiple scans, the operator re-positions a single Focus Scanner multiple times. Scans are transferred manually to a PC and are loaded into FARO Scene or BuildIT Metrology software. Individual scans are registered into one point cloud (again using target spheres to increase accuracy) and like with the automated approach, unused points are deleted using a clipping box. If BuildIT is not used, the point cloud is then imported into a metrology software (CAM2, Polyworks, etc.) where the required analysis is performed and a report generated. But as evidenced from the above, even in this scenario, the time savings are significant.
Out with the Old, in with the New
Automated or manual, either approach radically improves upon older methods of precision measurement. Under traditional workflows, manufacturers make a visual inspection for the absence, presence, positioning, and orientation of components – a time-consuming, error-prone exercise. The Focus Premium for 3DM applications eliminates much of this process-oriented bottleneck. Instead, customers receive absence, presence, positioning, and orientation reports, and even dimensional deviation reports from the point cloud loaded into the metrology software program. The result is the same precision with greater speed – but bypassing the accuracy level that is often more than what’s required for most inspection tasks of large parts.
The bottom line:
3D measurement equipment like the Focus Premium, the Quantum Max ScanArm and the Vantage Laser Tracker and their related software and accessory solutions like BuildIT Metrology, FARO CAM2 Software and Traceable 3D Targets, are the 21st century equivalents of the builders’, the welders’, and the solderers’, manual toolbelt. Rare is it for one tool to be the only tool to get the job done. Often, a variety of tools are required at each step along the manufacturing, assembly, inspection, and/or reverse engineering process.
Thus, in many cases a laser tracker and a laser scanner will be the ideal complementary solutions to complete a project.
When it comes to 3D Metrology, the expression “good enough is good enough,” might sound jarring at first. But when you drill down a little deeper, millimeters to microns, it’s clear that overly precise, time-consuming measurements can be just as disruptive as imprecise, inaccurate measurements.
Finding the right balance between speed and accuracy is where the conversation currently rests. And the FARO Focus Premium, with either automated or manual workflows, is the ideal compromise between these two extremes.
To learn more about how the Focus Premium can improve manufacturing processes, please don't hesitate to reach out by clicking on the link below.